The National Construction Code (NCC) includes mandatory regulations relating to condensation management. Several changes were introduced in 2019, and more were added in NCC2022.
Condensation management: What’s changed?
The most significant changes introduced by the condensation management regulations back in 2019, was that buildings in the colder BCA Climate Zones 6, 7 and 8 (all of the ACT, Tasmania and alpine areas, and parts of Victoria, WA, SA and NSW) should have vapour-permeable sarking on the outside of the primary insulation layer so that moisture can escape the building envelope.
Another change was a new requirement for ventilation of the roof space in the case of exhaust ventilation discharging into this area.
In 2022 the NCC introduced further changes, in particular for Class 1 buildings (including townhouses, detached and semi-detached dwellings), Class 2 buildings (sole occupancy units within apartments) and residential units attached to commercial buildings (Class 4).
These changes include:
- Increase in vapour permeance to wall sarking within climate zones 4 to 8.
- More stringent roof ventilation within climate zones 6, 7 and 8.
- Additional exhausting requirements for every climate zone.
Read more here.
These changes indicate that condensation problems are becoming more of a concern in residential builds, most likely as a result of buildings becoming more airtight to meet energy efficiency requirements.
How does condensation form?
The lower the air temperature, the smaller is its maximum possibility of holding moisture. The dew point is the temperature to which air must be cooled to become saturated with water vapour. When further cooled, the airborne water vapour will condense to form liquid water. When air cools to its dew point through contact with a surface that is colder than the air, water will condense on the surface. In built structures condensation becomes noticeable when beads of moisture appear on non-absorbent surfaces.
Condensation can occur on various surfaces in houses simply because of a low external temperature (such as during winter) or due to the activities of the residents, such as showering, cooking - or simply breathing! It is estimated that a family of four can generate up to 20 kilograms of water vapour per day inside a home.
Under ideal circumstances, excess moisture will escape from the interior of the house through air vents, open windows and openings such as the chimney. Ventilation is the first line of defence in controlling condensation and should be considered for the spaces in walls, under floors and particularly under roofs.
Unfortunately, natural ventilation is reduced inside many contemporary homes and moisture is retained inside the structure, especially when windows remain closed during winter, for security reasons or for noise control.
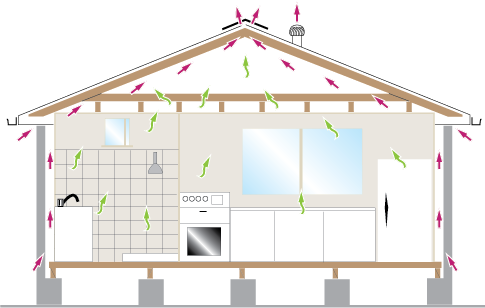
Risks associated with condensation in homes
In 2015 a scoping study into condensation in residential buildings was conducted by the Australian Building Codes Board (ABCB) and the results were alarming, indicating that up to 40% of new buildings in Australia showed signs of condensation and mould.
Condensation can lead to various costly and dangerous risks, including:
-
Health risks: Unseen mould growth behind wall linings and external cladding can be a health risk to the occupants, particularly the young or elderly, or those with asthma and/or allergies.
-
Visual deterioration: Bending or staining of plasterboard linings. Moisture trapped behind the linings can cause unsightly water stains and swelling. It can also lead to the blistering of paint and a musty smell inside the house.
-
Structural decay: Moisture trapped within the structure can have devastating results due to corrosion of metal structures, timber rot, loosening of nails as timber swells, and cladding rot or swelling.
Condensation and plasterboard
Plasterboard is susceptible to water damage and it is important to reduce condensation on all plasterboard surfaces. This is of particular importance in external plasterboard ceilings, such as in alfresco areas, carports, balconies and breezeways with plasterboard installed horizontally, or sloping away from the main dwelling.
At Siniat we recommend that no plasterboard is installed until the building is waterproof, particularly in coastal areas subject to sea spray. In external areas plasterboard must only be installed after the walls, windows, doors and roof covering have been completely installed and sealed.
Condensation on the face or the back of plasterboard can result in joint distortion, sagging, mould growth and fastener popping. To minimise the effects of condensation we recommend the following:
-
-
Choose a water resistant plasterboard such as watershield or trurock for external ceilings
-
Use moisture barriers, sarking and insulation according to the NCC regulations
-
Install eave vents, gable vents and roof ventilators in the roof cavity to improve ventilation.
-
Remove humidity from bathrooms and kitchens with properly installed extractor fans.
-
Use a quality paint system to provide protection against paint peeling and condensation soaking into plasterboard and compounds.
-
Ensure the building design controls condensation on the steel components so that they are not constantly wet.
-
In hot and humid climates where the building is air-conditioned to below the dew point of the outside air, the wall and ceiling framing members and internal linings should be fully protected by moisture barriers to separate them from the humid external air. The moisture barriers should be thermally insulated to maintain them at a temperature above the dew point.
-
Thermal insulation is recommended directly above the plasterboard. This will minimise the temperature difference between the plasterboard and outside air, limiting ceiling sag and mould formation by reducing condensation on the plasterboard.
-
To read more about condensation, ventilation and the care and use of plasterboard, download the Blueprint Technical Manual here.
For more information on Siniat products, contact us online, or call us on 1300 724 505.